Introduction
Adult-use cannabis became legal in Connecticut in 2021. Less that two years later, in January 2023, the market launched. To serve this additional market, the state's four existing medical producers had their licenses expanded and nine medical dispensaries converted their licenses to hybrid retailers. Since January, a further six dispensaries have converted their license to hybrid.
Currently, Connecticut has published regulations governing the testing of adult-use cannabis products. These tests include: cannabinoid analysis, heavy metals testing, pesticide residue and mycotoxin analysis, screening for pathogenic bacteria and fungi, and testing for residual solvents. Analysis requires sophisticated analytical instrumentation, compliance with state regulations, a quality system as dictated by ISO 17025, and, most importantly, highly trained scientific staff.
According to an article in MJBizdaily, “Recreational sales this year in Connecticut are projected to reach $300 million to $375 million, growing to $650 million-$800 million in 2026”. This expansion of the cannabis industry in Connecticut is resulting in an increased demand for product in the state and more grower licenses being issued. Currently there are four major growers in CT, and the state has awarded licenses to 16 microculture facilities. While many of these facilities are still coming on-line, more cannabis must be produced in the state to satisfy increased demand. Since every batch of cannabis product must be tested for potency and safety and must have an accompanying COA (Certificate of Analysis), the volume of lab testing in the state must certainly increase. As shown in Figure 1 from the Connecticut Consumer Protection government website, the existing and relatively stable medical cannabis market is quickly being overtaken by sales of cannabis products in the growing adult-use market.
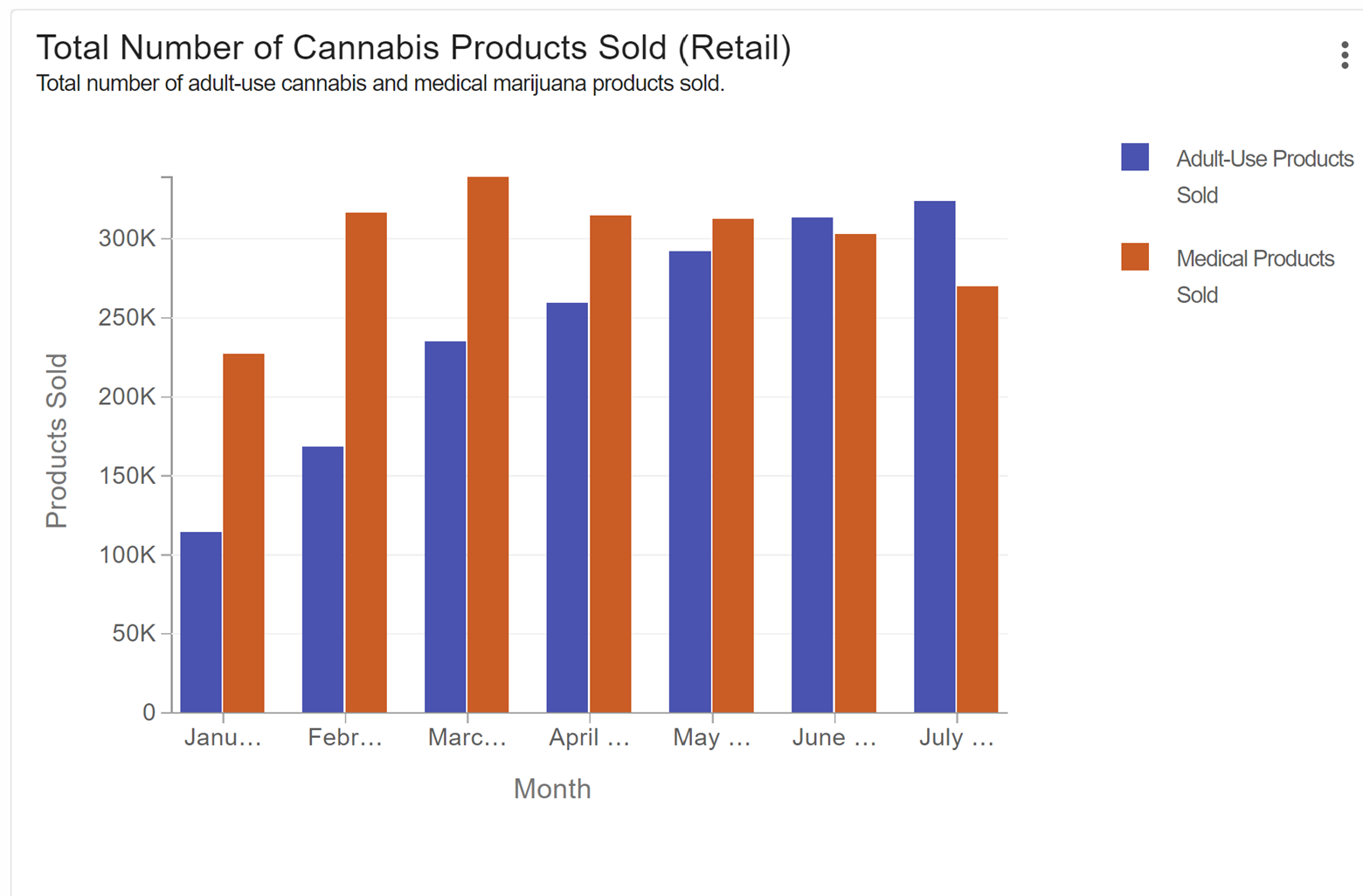
Figure 1: Number of medical vs adult-use cannabis products sold in CT since January 2023.
Image credit: Connecticut Dept of Consumer Protection Press release, 8/10/23.
This article will describe the current situation for cannabis lab testing in Connecticut with reference to the opportunities and barriers that both existing testing labs and new or startup labs face in this expanding market.
Existing test facilities
Until recently, there were two cannabis testing labs in the state, AltaSci Labs and Northeast Labs. AltaSci Labs in New Britain had been dedicated to medical cannabis testing and was preparing for adult-use product testing, but it closed its CT lab operations last spring. At the time of writing, Northeast is the only operating cannabis testing lab in Connecticut.
I visited Northeast’s new Rocky Hill facility and interviewed its lab director, Dr. Zachary Cannone. Dr. Cannone has a PhD in chemistry and he directs some 20 chemists and technicians who perform the entire battery of tests required by the state. The Rocky Hill lab is modern and well equipped. Its instrumentation includes a liquid chromatography with tandem mass spectrometry (LC-MS-MS) system, a gas chromatography-mass spectrometry (GCMS) system with Headspace, an inductively-coupled plasma mass spectrometry (ICP-MS) instrument, an ultra-performance liquid chromatography with an ultra violet detection system (UPLC-UV), a quantitative polymerase chain reaction (qPCR) instrument and a fully equipped lab for plate-based microbiology.
Dr. Cannone told me that Northeast Labs (NE Labs) has a long history in Connecticut, going back to the '70s. Its original purpose was to perform analytical testing for environmental and other sample types. This experience proved invaluable when the medical cannabis market opened in 2012, since it had the scientific expertise and many of the instruments required for testing in the new cannabis market.
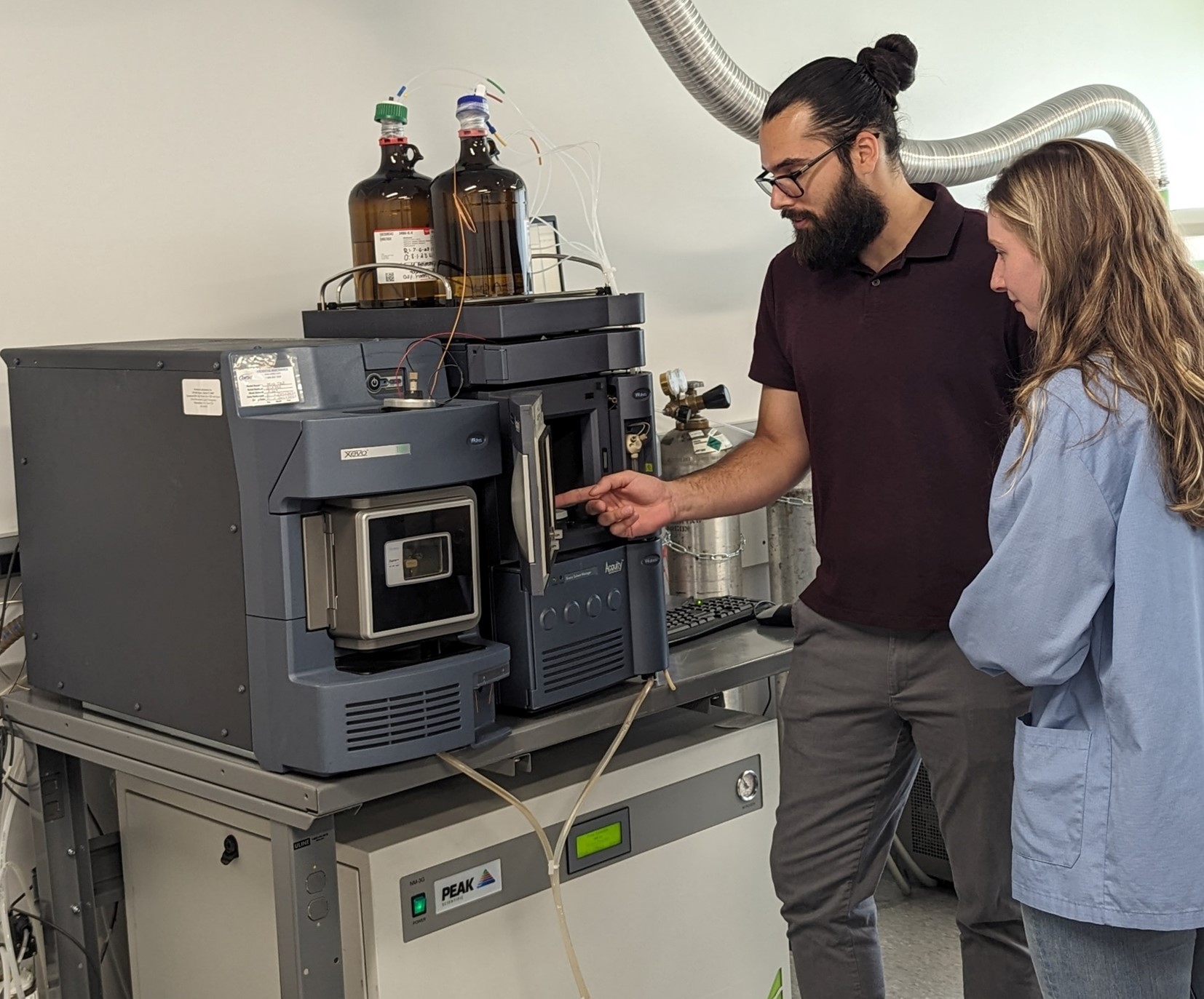
Figure 2: Dr. Zachary Cannone, director of Northeast Labs, Rocky Hill, CT, works with Technician Brooke Hillman on the LC-MSMS system used to determine pesticide residues in cannabis samples.
Image credit: Northeast Labs.
When asked about the requirements imposed by the new Connecticut regulations and the technical challenges of complicated analytical tests, Dr. Cannone told me that the current CT regulations were very strict, more so than those in other states. Northeast’s biggest technical challenge has been to keep up with new techniques and regulatory requirements. For example, it must quantify 21 Category I pesticides, 45 Category II pesticides as well as five mycotoxins by LC-MSMS. This requires long high-performance liquid chromatography (HPLC) gradient runs and complex multichannel MSMS monitoring along with instrument polarity changes, which place a high demand on analysts and instrumentation.
Cannone’s lab is gearing up training new technicians and preparing to install new instrumentation and upgrade software to meet the expected increase in sample volume. When asked about the lab’s preparations, Cannone told me:
“We have been onboarding many new techniciansand we are also tentatively planning a small expansion into the adjacent space of the building. I have some new instruments being prepped for delivery and I am also working to overhaul our laboratory information management system [LIMS] system to integrate our workflow.”
Cannone also said that sampling and transport of samples has become the lab’s responsibility, as current regulations require that sampling/transport had to be done by lab employees.
Regulation and enforcement
Connecticut regulations require ISO 17025 compliance for all certified cannabis testing labs. According to Dr. Cannone, securing this certification for NE Labs was very challenging; but the lab succeeded and its follow-up ISO audit was successful with only minor findings.
The cannabis lab business in CT is regulated by the Department of Consumer Protection (DCP), which are ultimately responsible for testing labs and enforcement of the regulations. Kaitlyn Krasselt, DCP Director of communications, told me that all cannabis products submitted to the department for brand approval must have first passed all required safety tests. Since branding is expensive, a product that failed one or more tests would not be submitted, and DCP would not learn of this product. There are provisions in the state guidance for remediation and retesting, but these processes are complicated and the latter require testing by a second lab when the retest results disagree with the original results.
“Remediation is not allowed for medical products," Krasselt told me. “In our adult-use program, if a business wanted to remediate a product, they would need to seek approval from the commissioner first, and if approved, additional testing would be required. To date, nobody has sought approval for remediation.”
Cannabis potency and safety tests are cross checked by the Analytical Lab at the Connecticut Agricultural Experiment Station (CAES) in New Haven. I spoke with Dr. Christian Dimkpa, Analytical Lab Director at the Connecticut Agricultural Experimental Station (CAES), about its lab monitoring activities. Dr. Dimkpa told me that his lab analyzes a randomly selected subset of samples tested in the state and their team compares their test results with those listed on the COAs. The tests that they verify include cannabinoids and potency, pesticides, and heavy metals. Mycotoxins will come online at CAES in the near future. Dr. Dimkpa said that the re-analyses have so far yielded good agreement with label claims, with a difference in potency numbers only in the range of 3%. According to Dr. Dimkpa, pesticide residue testing by CAES has not found any listed pesticide quantifying over the regulation’s threshold concentrations.
Generally, the testing operations in CT seem to be running well, although there is a concern that having a single testing lab puts all the state’s testing in one basket. As such, a lab accident, prolonged power outage, or a business collapse could delay or stop testing services. Dr. Dimkpa said that, if such an event took place, CAES would have to take up the slack until the private lab came back into service. When I asked Dr. Dimkpa why more testing labs were not coming online, he said that accreditation was time-consuming, given that experts are hard to find, and that equipment was very expensive to purchase and maintain. Regarding instrumentation, Dr. Cannone from NE Labs told me that, besides their high price, instruments were difficult to come by, and had very long delivery times. Some of these problems may be due to recent chip shortages and supply chain issues.
Regulation of cannabis testing is done by the Connecticut Department of Consumer Protection
I received direct answers to several of my questions from Dr. Rodrick Marriott, the Director of Drug Control for the state's DCP, regarding the current state of cannabis testing in Connecticut. The list of questions and his replies (RM) are given below:
Q: What is the current cannabis testing environment in the state?
RM: We currently have one laboratory that appears to be able to efficiently manage the current testing volume.
Q: Is there sufficient testing capacity with qualified labs?
RM: We believe that we have enough but would like to see more qualified laboratories enter the market, particularly as the market expands to new cultivation and manufacturing.
Q: Are the growers and microculture facilities in the state satisfied with this testing service and sample turnround?
RM: We have heard no specific complaints to date.
Q: Have you found any unsafe levels in tested products? Heavy metals, pesticide residues, mold or bacteria?
RM: The laboratories have failed some samples that they have taken from the cultivation facilities. We do not have specific numbers at this time.
Q: What, if any, recommendations do you have that might improve CTs cannabis testing program and improve safety for consumers?
RM: We continue to evaluate the emerging science and the national standards that are being developed as well as what other states have been doing. As we review them, we will likely add them to the policies and procedures for the cannabis industry. In the previous legislative session, a separate laboratory license was created to help provide the industry with a more clear path forward.
Recent legislation, CT Public Act 23-79 (sect 16), requires that all new cannabis testing labs established after July 1, 2023, apply for and receive a separate testing license through the CT DCP. This licensure will ensure registration with DCP, and it will carry with it the requirement for full compliance with CT’s cannabis testing regulations. There is a provisional fee of $500 for the license and a fee of $1000 upon receipt of an approved license.
Dedicated cannabis lab startups: a false start in Fairfield County, CT
The potential problems posed by a single test lab in the state could be avoided by the establishment of new labs that could absorb increased sample volume and also provide a safety valve in the case of failure or down time of other state labs. The most important incentive for cannabis test lab startups is that the increased testing for the adult-use market will generate incremental business. With the anticipated 16 micro-cultivators coming up to speed and additional production from the four major growers, a large increase in testing demand is expected. Clearly, a startup lab with good analytical chemistry expertise and sufficient funding will have great market opportunities, so then why have there been no new labs appearing in Connecticut?
The author can reference his own recent experience as a primary consultant for a startup test lab in Western Connecticut. This effort was reasonably well funded with a primary partner providing $1.6M and outside funding promising $3M. The original business plan looked acceptable, so the group, we will call XYZ Labs, began shopping for a location and equipment during the winter of 2022.
Housing the lab
XYZ opted to buy its own building to house the lab rather than to lease lab space, so as not to be at the mercy of a landlord. A building to permanently contain the facility ranged in price from $600K to $2.2M. There were also considerable difficulties encountered in obtaining permission from planning and zoning in most of the towns, because officials were reluctant to allow a building to be repurposed as a cannabis lab. Letters of intent and emails were sent, and follow-up phone calls were made to local officials in eight municipalities. In the end, only two large towns in Western Connecticut agreed to allow XYZ to set up shop.
Procuring major instrumentation
The group decided to purchase new instruments with service contracts to ensure reliability and performance rather than out-of-warranty used instruments with potential problems. We determined that using a single vendor for the instruments would help to ensure continuity of service/support, and it would also provide uniform software interfaces, simplifying data analysis and reducing learning curves. Agilent was chosen for all instruments – bar the LC-MSMS – because it is well invested in the cannabis testing market and offers complete packages supporting all of the currently required analyses. The company also has a good service and support presence in north-east United States. The Sciex LC-MSMS was chosen because of its sensitive quantification capabilities and our experience that it can maintain ion path cleanliness despite dirty matrices, a very important consideration for cannabis samples. Other major instrument venders certainly manufacture quality equipment; Agilent and SCIEX were chosen based upon our investigations and previous lab experience.
The estimated costs of major instrumentation and service contracts put costs near $1M, Table 1.
Table 1. Major Instrument Costs and Service contracts
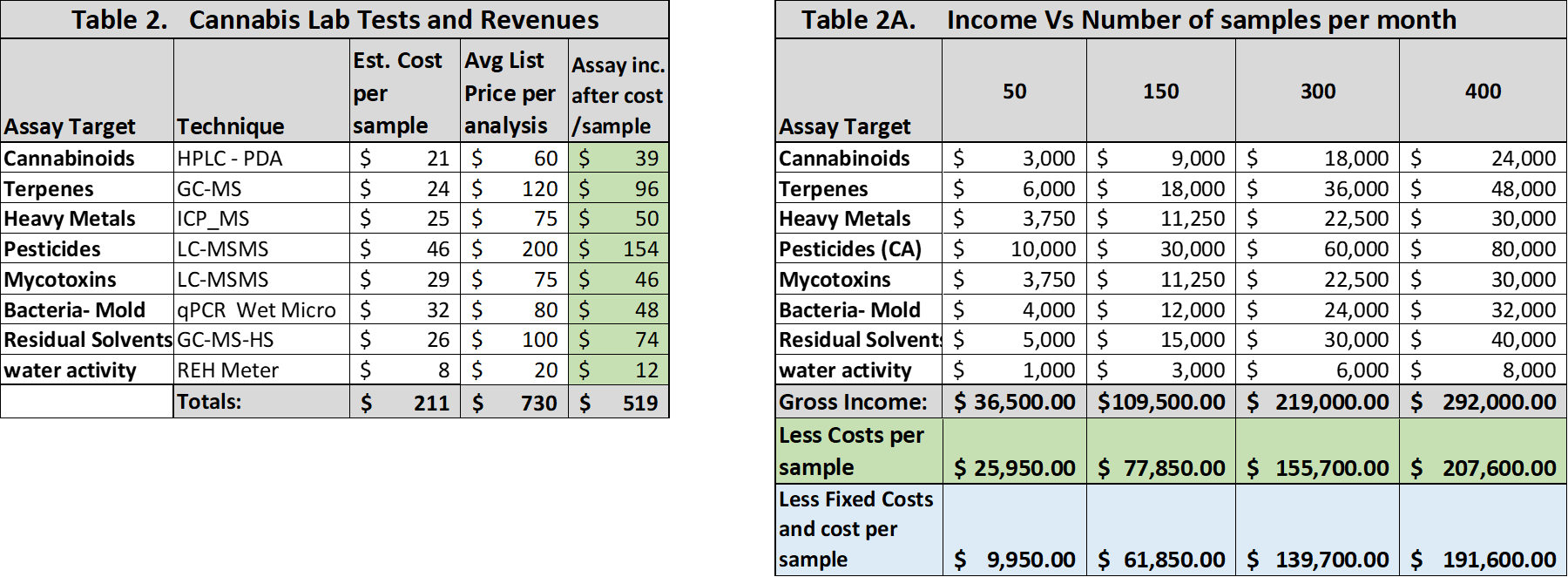
Note that the service contract costs were estimated at 10-13% of the instrument cost per year after the one-year warranty period. There is little choice than to have these contracts, since repairs and parts are prohibitively costly without them.
Associated lab equipment
Additional costly equipment required included: a microwave digestion system for ICP-MS samples, a cryo-mill for preparation of edible samples, a refrigerated sample centrifuge, a fully equipped and isolated microbiology lab with laminar hood, autoclave and incubators, a vault for sample storage, a sophisticated security and lighting system, and a dedicated LIMS system for data and “seed-to-sale” compatible sample tracking. On top of these expenses, startup costs for other small equipment, supplies, cabinets, hoods, heating, ventilation, and air conditioning (HVAC) systems, gasses. A deionised water system and specialized utilities brought the total initial investment up to about $3.2 M, exclusive of real estate.
Certification and quality system: ISO 17025
All labs must have a verified quality system, guaranteed by a quality control employee and supported by ISO 17025 certification. ISO 17025 certification expenses include costs for assessment, training, documentation, proficiency testing, computers, software and consulting that can come to more than $320,000 for a reasonable sized lab (20 employees) with substantial ongoing costs. Computers, server and software costs, a bar coding system for sample accession, inventory and lab workflow interfaces to the instruments and LIMS system required still more investment.
Employees, salaries, and retention
Hiring and retention of competent laboratory personnel, instituting training and continuing education programs for them is a final very important cost consideration. Laboratory scientists and technicians must be highly competent, dedicated, and trustworthy in order to make the effort successful. Such professionals are difficult to find, and they must be incentivized to become long-term employees. This requires competitive salary offerings with good benefits, supplementation with ongoing training programs, and funding for attendance at conferences, symposia, along with continuing education.
Revenue and ROI
On the owner/capital investor side is return on investment (ROI), initial cash burn rate, and payback of cash investors. In the table below, we calculated projected revenue based upon cost per sample and extended this to various numbers of samples analyzed per month. We corrected these incomes for running costs (analysis time, operator time, supplies and reagents) for each assay, but not for property costs, taxes, and utilities (Table 2).
Table 2. Projected revenue from the full cannabis test panel vs samples analyzed per month.

Table 2 (above) shows our calculation of assay income corrected for running costs (materials, reagents, operator time). For a full test panel, this yields a margin of about 71%. Monthly income, corrected for assay costs and projected for number of samples analyzed per month, is shown in Table 2A in green shading. The use of autosamplers, 96-well plates, overnight runs and other automation methods provides some incremental savings as sample volume increases, particularly for chromatographic assays; but this is not as applicable for other methods such as plate-based microbiology requiring overnight incubations and individual colony counting. Further, sample digestion for ICP-MS and other sample prep procedures for various inhaled and ingestible forms can be complicated and time consuming, negatively offsetting some of the advantages of instrument automation. While many published methods are available, each new sample type can present a unique sample prep challenge, often requiring additional development time and sometimes resulting in a new extraction procedure.
When fixed costs (taxes, HVAC, utilities, security, and maintenance) along with support staff salaries and benefits are calculated (Table 2A, right), a monthly expenditure of about $16K is required. The bottom line is hit hard by these expenses (blue shading), and high-sample throughput, unlikely during the first two years of operation, is needed for optimal profit. The major investor determined that the cash flow would be insufficient to provide the required payback for the investor and business partners. Further, it was almost impossible to secure additional credit in conventional financial channels, since the federal illegality of cannabis blocks most bank loans and makes other loan types very expensive.
Unfortunately, the XYZ Labs project was cancelled. The takeaway from this experience is that a startup cannabis testing lab needs to be solidly financed with a minimum of $5-6M, and the investors need to be capable of tolerating at least two years with no profit and significant cash burn rates. Getting such a lab established is a long and expensive process that needs major effort, much technical expertise, strong funding, and investor patience.
Hybrid labs
Given the difficult financials of a dedicated cannabis lab startup, it might be that one could arise less painlessly as an extension from an already-established analytical lab with existing instrumentation, chemistry equipment, personnel, and scientific expertise. This was certainly the case for NE Labs.
I spoke to Jeff Smith, operations manager for CET Environmental Labs in Stratford, CT. CET is a mid-size analytical lab with 18-21 scientific staff. Management at CET considered doing cannabis testing, but they determined that it would cause too many changes in their operating system, requiring new equipment (adding HPLC to a primarily GC-based lab) with major changes in their lab workflow and in their LIMS system, especially from a regulatory standpoint. They were particularly concerned about tracking cannabis samples, which would require maintaining sample balance sheets to within tenths of a gram. Smith said that their lab is now facing large increases in other analyses, such as per-and polyfluoroalkyl substances (PFAS), and they would need to pull too many resources off of their regular business to support cannabis testing. As such, CET decided not to take the leap.
Conclusions
The “failure to launch” fate of the XYZ lab startup was caused by a combination of factors: expensive CT real estate, high priced instrumentation, extensive regulatory and security requirements, personnel expenses, and inability to secure lower cost financing. One of the most important reasons was the inability of the major investor to defer repayment and absorb cash burn during the lab’s establishment period. The current cannabis testing situation in Connecticut is one that appears to be financially difficult for new ventures, except for those willing to provide $5-10M in startup capital with the patience to tolerate high initial cash burn rates and to defer payback.
Zachary Cannone of NE Labs told me that their company has been long established in the environmental and general analytical fields, and this has done much to ensure their continued success. They are currently active in environmental and food safety analysis, both microbiological and chemical, which provides consistent testing income and helps to supplement income from their cannabis testing program. Established analytical labs in the state would appear to have a head start for cannabis testing, but at least one lab, CET, was not willing to branch out to cannabis because it would cause a dramatic change in its business model. Other such labs in the state with different circumstances may feel able to enter the cannabis market, as the need is certainly there.
The current laboratory testing landscape in Connecticut is working, but there are inherent risks to having only one testing lab in the state. The state CAES analytical lab seems to be keeping up with cross checks, and it has found good agreement with COAs generated by NE Labs. Despite this working system, there are risks to the market should there be any failures or downtime that could disrupt testing. Current market conditions would certainly favor the establishment of additional cannabis testing facilities in Connecticut. To undertake such a venture is expensive and technically daunting, but both the opportunity and the need are there.
*This article was updated on September 6, 2023. A previous version of the article alluded that medical dispensaries opened in Connecticut following the legalization of adult-use cannabis in 2021, when four such dispensaries were already operating at that time.
The article also incorrectly credited Dr. Rodrick Marriott as the commissioner of Connecticut's Department of Consumer Protection. His title (and the spelling of his name) have since been amended.